Safety Programs - RAVS®
Expedited Program Creation and Guaranteed Compliance, just one call away!
Safety Programs
Ready to Submit!
- Detailed Customization
- Expedited Delivery
- Word and PDF
- Safety Manual Adaptable
- Safety Sign-In Sheet Included
- Pre-qualification Ready
- Guaranteed ISNetworld® Appruval
-
Written to satisfy prequalification standards in:
Avetta®, Appruv®, Veriforce®, Vero®, Ariba® and others
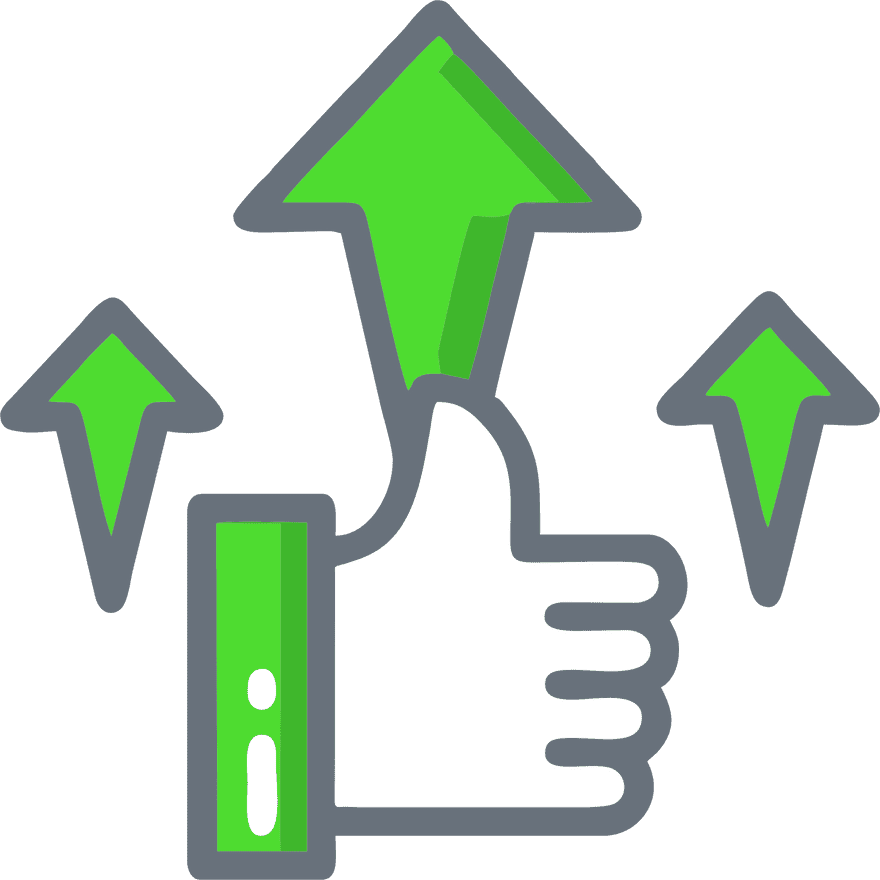
HSE Programs with Cascade QMS
- Set Safety Expectations
- Establish Employee/Management Expectations
- Provides transparency for Hiring Clients
- Protects Company Assets
- Meet Client Compliance Requirements
- Employee Development
- Streamlines Employee Onboarding and Orientation
- Assists with Grade Mediation
Our team of consultants are dedicated to your business’ success. We operate quickly and provide quality safety materials to ensure your compliance is met and best possible grades are achieved in ISNetworld® and other major vetting systems. We’re dedicated to helping your company comply with the safety demands of large corporations such as Amazon®, Honeywell®, Pfizer®, Disney®, JBS®, Energy Transfer® and many more!
Call us now at 1-855-792-5722 to get started.
Safety Program FAQs
RAVS® stands for “Review and Verification Services,” and it is a component of ISNetworld® (ISN), a global platform used by companies to manage contractors and suppliers. ISNetworld® provides a centralized database for connecting organizations with contractors and suppliers who meet specific safety, insurance, quality, and regulatory standards.
Within ISNetworld®, RAVS® refers to a set of safety-related documents and programs that contractors are required to submit for review and verification by hiring clients. These documents demonstrate that a contractor’s safety programs and practices align with industry standards and regulatory requirements. RAVS® helps hiring clients assess the safety performance and compliance of their contractors.
Typically, RAVS® documents cover various aspects of safety management targeted at each contractor and supplier’s industry.
A written safety program is the broader framework of safety policies and procedures within an organization, while RAVS® specifically refers to the set of safety-related documents submitted by contractors for review and verification by hiring clients, particularly within contractor management platforms. RAVS® is a subset of the overall written safety program, focusing on specific documents that demonstrate a contractor’s adherence to safety standards.
OSHA Compliance Programs:
- Injury and Illness Prevention Program (IIPP)
- Hazard Communication Program (HazCom)
- Respiratory Protection Program
- Lockout/Tagout (LOTO) Program
- Confined Space Entry Program
- Bloodborne Pathogens Program
- Hearing Conservation Program
- Fall Protection Program
- Electrical Safety Program
- Personal Protective Equipment (PPE) Program
- Machine Guarding Program
- Hazardous Energy Control Program
Environmental Health and Safety (EHS) Programs:
- Emergency Response and Evacuation Plan
- Spill Response and Prevention Program
- Hazardous Waste Management Program
- Air Quality Control Program
- Water Pollution Prevention Program
- Stormwater Pollution Prevention Plan (SWPPP)
- Environmental Management System (EMS)
Construction Safety Programs:
- Construction Safety Plan
- Excavation and Trenching Safety Program
- Scaffold Safety Program
- Crane Safety Program
- Fall Protection Plan for Construction
Transportation Safety Programs:
- Fleet Safety Program
- Defensive Driving Program
- Driver Fatigue Management Program
- Hazardous Materials Transportation Program
Industrial Hygiene Programs:
- Exposure Control Program
- Chemical Hygiene Plan
- Indoor Air Quality Program
- Heat Stress Prevention Program
- Asbestos Management Program
Fire Safety Programs:
- Fire Prevention Plan
- Fire Emergency Response Plan
- Hot Work Permit Program
Workplace Violence Prevention Program
Injury and Illness Management Programs:
- Return-to-Work Program
- Recordkeeping and Reporting Program
Process Safety Management (PSM) Program (for certain industries)
Employee Wellness Programs:
- Health and Fitness Programs
- Stress Management Programs
- Ergonomics Program
Lockout/Tagout (LOTO) Program
Electrical Safety Programs:
- Arc Flash Hazard Analysis
- Electrical Hazard Recognition and Control Program
Radiation Safety Program
Bloodborne Pathogens Exposure Control Plan
Hazardous Materials Management Program
Emergency Action Plan (EAP)
Personal Protective Equipment (PPE) Program
Pandemic Preparedness Plan
Pest Control Program
Traffic Control Safety Program
Asbestos Management Program
Lead Safety Program
Compressed Gas Safety Program
Hearing Conservation Program
Respiratory Protection Program
Machine Guarding Program
Heat Stress Prevention Program
Biological Safety Program
Crisis Management and Communication Plan
Hazardous Communication Program (HazCom)
- Tower Safety
- Working at Heights
- Radio Frequency
This list covers a wide range of safety programs, but it’s not exhaustive. Specific programs applicable to a particular organization will depend on its industry, operations, and compliance requirements. Companies should always refer to relevant regulations and industry standards when developing and implementing safety programs.
This is not the complete list of programs available from Cascade QMS. Please reach out for our library of programs!
The frequency of safety training for employees can depend on various factors, including the nature of your industry, the specific hazards associated with your workplace, regulatory requirements, and the complexity of your safety programs. Here are some general guidelines to consider:
Initial Training:
- All employees should receive comprehensive safety training when they are initially hired or assigned to a new job or task. This training should cover essential safety information, emergency procedures, and the specific hazards associated with their roles.
Regular Refresher Training:
- Regular refresher training is important to reinforce key safety principles and update employees on any changes in safety procedures, regulations, or equipment. The frequency of refresher training can vary but is often recommended annually.
Task-Specific Training:
- If employees are assigned new tasks or responsibilities that involve different safety considerations, provide task-specific training before they undertake those duties. This ensures that they are aware of the specific hazards associated with their new tasks.
Changes in Equipment or Processes:
- Whenever there are significant changes in equipment, processes, or workplace conditions that could affect safety, employees should be promptly trained on the new procedures and precautions.
Incident-Specific Training:
- If there is an incident or near-miss in the workplace, use it as an opportunity to reinforce safety training. Conduct additional training addressing the specific issues that led to the incident to prevent recurrence.
Regulatory Requirements:
- Be aware of any specific regulatory requirements for safety training in your industry. Some regulations may mandate specific training intervals or topics.
Feedback and Evaluation:
- Regularly assess the effectiveness of your safety training programs. Encourage feedback from employees, and use evaluations and incident reports to identify areas that may require additional training.
Seasonal Considerations:
- In some industries, seasonal changes or specific operational cycles may warrant more frequent safety training. For example, construction sites may have different safety considerations during winter months.
Remember, these are general guidelines, and the specific needs of your organization may vary. It’s crucial to conduct a thorough risk assessment, stay informed about industry best practices, and comply with any regulatory requirements applicable to your business. Regularly reviewing and updating your safety training programs ensures that employees remain aware of potential hazards and are well-prepared to work safely.
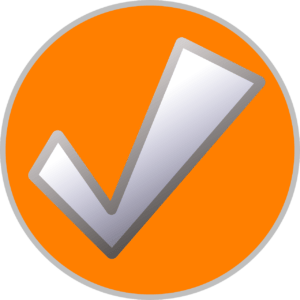
Let's customize a solution for you!
Health Safety Environmental
Written Programs
No company is too small to establish a solid safety culture! In fact, good safety practices are extremely crucial for small business as one injury can have major impacts on your EMR (experience modification rate), workers compensation and client relationships.
Safety investments can be quite expensive. Here at Cascade QMS we are dedicated to providing quality safety management solutions with a small business budget in mind. Cost should never come between you and safety. One of the biggest discussions we have with our clients begins with the question: Is ISNetworld® worth the investment? More often than not, the answer is a resounding YES!
Of course, there are many things to consider when considering if your company wants to entertain more projects and develop a solid safety culture, that’s why we offer free consultations. Our Cascade QMS consultants will ask specific questions and provide information to help you make the decision that’s best for your company. No two companies are the same.
One thing is certain, contracting Cascade QMS to set your account up and maintain it is a sure win. Our experienced staff is thorough and efficient. Combine our services with our extensive safety library and you have a wining recipe for your company’s safety compliance. Your time is too valuable to quote. We’ll handle the paper work, while you do what you do best!
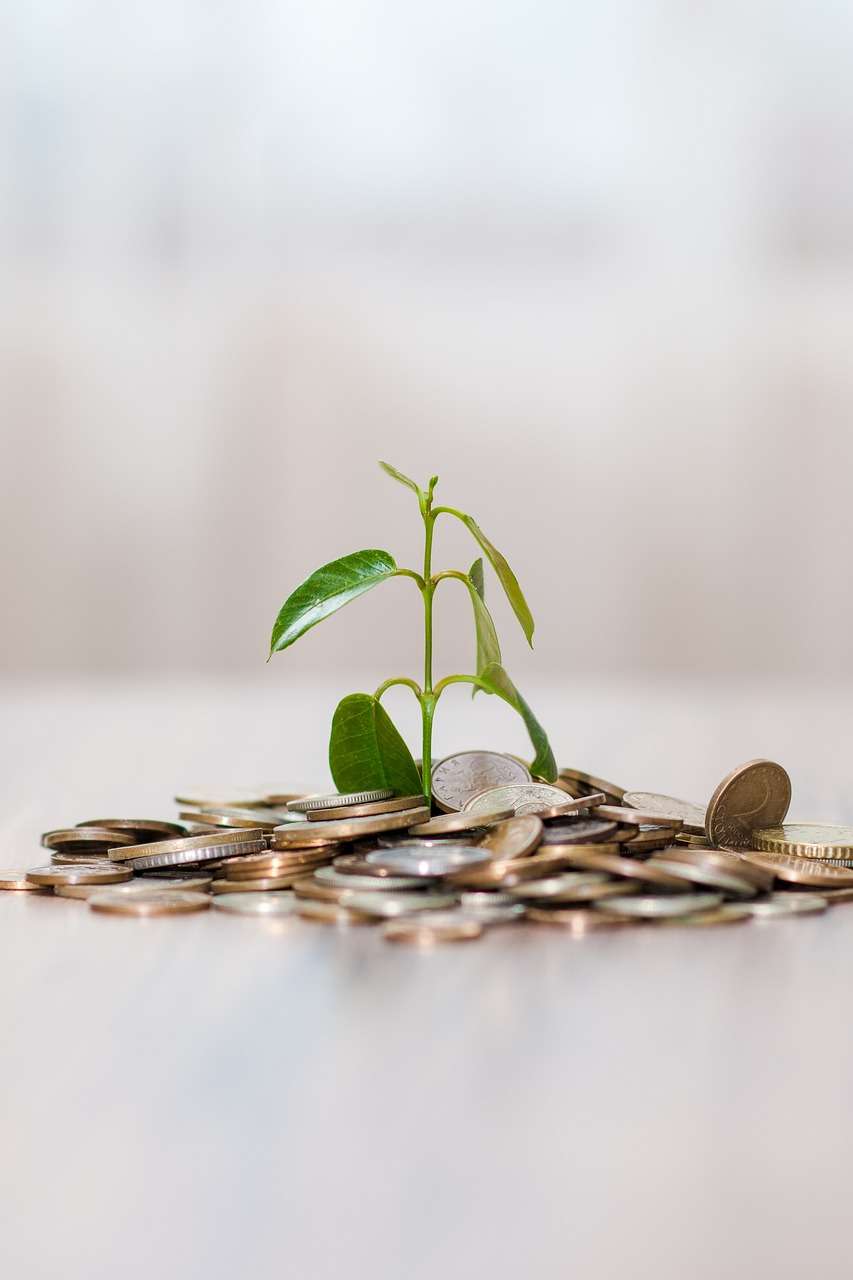